- Hard Hats - Protecting the head from falling objects or impact
- High-Visibility Vests - Making workers more noticeable to others on site
- Safety Glasses - Protecting the eyes from particles or debris
- Gloves - Protecting hands from cuts, abrasions, and chemicals
- Earplugs/Earmuffs - Reducing loud noise levels to protect hearing
- Respirators - Filtering out harmful particles and chemicals from the air
- Safety Harnesses - Preventing falls from elevated areas
- Boots with Steel Toes - Protecting feet from heavy objects or sharp objects
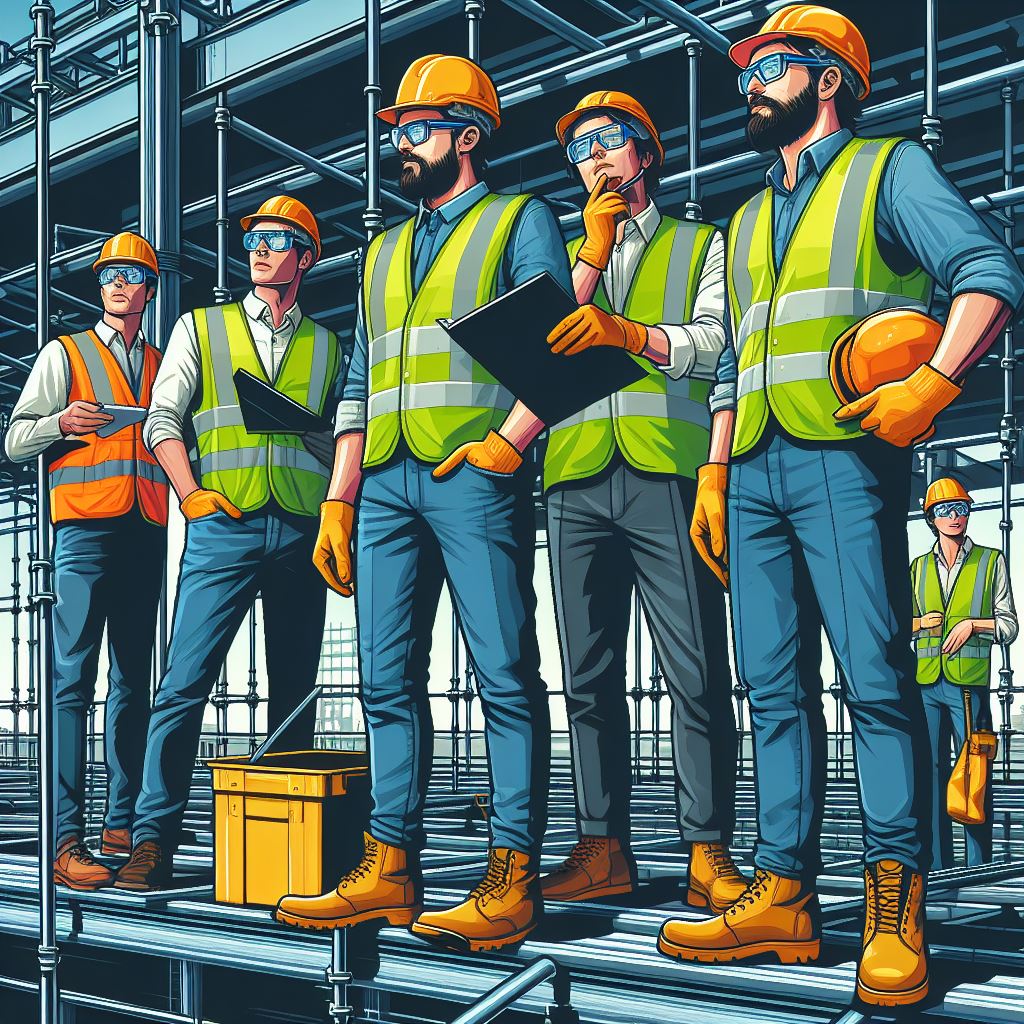
The Vital Importance of Safety Equipment in a Construction Site
Construction sites are notoriously known for being high-risk environments. With various heavy machinery, hazardous materials, and constantly changing conditions, it is no surprise that accidents can happen at any moment. The safety of workers should be the top priority for any construction company, and one of the most effective ways to ensure the well-being of employees is by implementing proper safety equipment.
What is Safety Equipment?
Safety equipment refers to any gear, clothing, or devices that are designed to protect workers from potential hazards and injuries in the workplace. This can include hard hats, high-visibility vests, safety glasses, gloves, earplugs, and more. Depending on the specific job and tasks, different types of safety equipment may be required. The purpose of safety equipment is to minimize the risk of accidents and injuries, ensuring a safe and healthy environment for workers.
Legal Requirements
"Safety first" must be a company's motto, especially in the construction industry. In addition to being a moral responsibility, implementing safety equipment is also mandated by law. Both federal and state laws have strict regulations and standards for workplace safety, including those specifically for the construction industry. Companies that fail to comply with these regulations can face severe penalties, including fines, lawsuits, and even shutdowns of the project.
To avoid such consequences, companies must ensure that they are following all safety protocols and providing their workers with the necessary equipment. This not only protects the employees but also protects the company from legal repercussions.
Preventing Accidents
Statistics show that an alarming number of workplace accidents happen in the construction industry. According to the Occupational Safety and Health Administration (OSHA), one in five worker fatalities in 2019 was in construction. The most common causes of these accidents include falls, being struck by objects, electrocutions, and caught-in/between incidents.
By implementing safety equipment, many of these accidents can be avoided. Hard hats can protect workers from falling objects, high-visibility vests can make them more visible to avoid being struck by moving vehicles, and safety harnesses can prevent falls from high elevations. Other equipment such as gloves, eye protection, and earplugs can also prevent injuries from specific tasks.
Protecting Workers' Health
Construction workers are exposed to various health hazards on the job. Exposure to dust, chemicals, loud noise, and extreme temperatures can all take a toll on their physical well-being. Prolonged exposure to these hazards can lead to serious health issues such as respiratory problems, hearing loss, and skin diseases.
Safety equipment serves as a barrier between workers and these health hazards. For example, masks can protect workers from inhaling harmful dust particles, and earplugs can protect their hearing from loud noises. Additionally, personal protective equipment (PPE) can also prevent injuries and infections, such as gloves preventing cuts and abrasions and masks preventing the spread of respiratory illnesses.
Increasing Productivity
In addition to protecting workers' safety and health, safety equipment can also increase productivity on construction sites. Accidents and injuries can not only harm workers but also disrupt the workflow. When an accident happens, it can halt the entire project, resulting in delays and additional costs.
By implementing proper safety measures and providing workers with appropriate equipment, companies can reduce the risk of downtime caused by accidents. For example, using safety harnesses while working at heights can allow workers to focus on the task at hand instead of worrying about falling. This leads to increased efficiency and productivity.
Boosting Employee Morale
Aside from the practical benefits of safety equipment, its implementation also shows a company's care and concern for its workers. Employee morale is crucial in any workplace, as it directly affects their motivation and performance. By prioritizing their safety, companies can boost employee morale, creating a positive work environment.
Employees who feel that their well-being is valued by their employer are more likely to be satisfied with their job and have a higher level of commitment and dedication. This can ultimately lead to improved performance and increased job satisfaction.
Types of Safety Equipment
The types of safety equipment required in a construction site depend on the nature of the work. Some common examples include: